You can download the pdf version HERE
Case study of a practicable, risk-based solution in response to Recognised Standard 22.
S Amor1 and A Beasley2
1. MAusIMM, Director, Zen Meerkat Pty Ltd, Brisbane Qld 4000. Email: amor.steve@outlook.com
2. Director, Jarah Corporate Pty Ltd, Brisbane Qld 4000. Email: anthony@jarahcorporate.com.au
ABSTRACT
This paper provides an example of how industry can respond to the implementation of new regulatory approaches to mining risk, health and safety by adopting a robust, practical, software-based approach to the management of risk accountabilities in terms of competence, experience and suitability for obligations and responsibilities, as required in Queensland Coal Mining operations due to the introduction of Recognised Standard 22 (‘RS22’; Resources Safety and Health Queensland, 2021).
Based on the authors’ experience from working with several Qld mine operations, it offers a snapshot of the experiences, approaches and reservations faced collectively by industry as a result of the introduction of RS22.
Several challenges exist within the detail of RS22, leading to varied interpretations, implementation strategies and overall compliance between mine sites. Arguably the single biggest challenge identified has been how to find a balance between compliance and practicality – considering cost, operational interruption, available pathways for delivery of competence, ongoing compliance and value adding to the business operations and people.
Software-based solutions are increasingly being relied upon to address the introduction of new regulatory approaches and the significant administrative load placed on mining operation Site Senior Executives (‘SSE’) due to RS22 means this case is no different. This is further complicated given the continuous, ongoing changes with the site management structure witnessed by the authors across each of the mining operations as a result of continuous changes to personnel, the site risk profile and an overall mining industry uncertainty of how to respond to RS22. The stringent reporting/notification requirements under legislation compounds this further.
The approach put forward by the authors is a well-considered rationale and approach to the application of training and skilling; and equally how to ‘future proof’ the coordination of site training needs around changes to the Management Structure, the Risk Register, skilling processes and succession planning.
A brief investigation of other legislative frameworks concluded this approach would likely meet or exceed expectations of jurisdictions across Australia and overseas, making this a highly flexible approach for establishing a competent Management Structure to provide safe systems of work.
INTRODUCTION
Recognised Standard 22 (‘RS22’; Resources Safety and Health Queensland, 2021) defines a substantially new way for the Site Senior Executive (SSE) to develop and maintain a management structure for the purpose of development and implementation of the Safety and Health Management System (SHMS). It requires the SSE to delegate responsibilities associated with the management of risk specific to each mine and determine the competency requirements of all Management Structure positions in relation to the site risk profile.
This approach differs from the common practice prior to the gazetting of RS22, where there was little requirement related to roles in the statutory management structure to hold specific technical competencies related to risk and little recognition in relation to role specific and mining industry experience.
Several challenges exist within the detail of RS22, leading to varied interpretations, implementation efforts and overall compliance between mining operators observed by the authors. Arguably the single-biggest challenge identified has been how to find a balance between compliance and practicality – considering cost, operational interruption, available pathways for delivery of competence, ongoing compliance and value adding to the business operations and people.
METHOD
The authors worked closely with several mine operators throughout Queensland to implement RS22 at their sites. This report offers a snapshot of the understanding, challenges, approaches and reservations faced collectively by industry because of the introduction of RS22.
A methodical, practical, documented system has been developed to initially meet and then deliver ongoing compliance. The deliverable items developed during the process include:
· Site Material Unwanted Event (MUE) Rationale.
· MUE Matrix.
· Competency hierarchy and matrix.
· Statutory Management Structure document.
· Tailored Letters of Appointment per Management Structure role.
· Input into the site Training Needs Analysis and Plan specific to risk, roles and responsibilities.
· Maintenance of the framework/ongoing compliance tools.
FINDINGS
The key findings from the case study sites were as follows.
Industry training package deficiencies
RS22 creates an expectation that the RII (Resources and Infrastructure Industry) training package, qualifications and units of competency will be referenced. The reality found by the authors however is one where mining operations are not able to comply with this expectation, as many required topic area units are missing within the RII package, or they are simply not available on offer by any Registered Training Organisation (RTO).
For example, the MUE related to ‘vehicle interaction’ has the following RII units of competency available that the SSE may be consider:
· AQF level 4: RIIMPO403D – Monitor interaction of heavy and light vehicles and mining equipment (available via RTO’s for this Certificate 4 level unit).
· AQF level 5: RIIMPO502D – Manage the interaction of heavy and light vehicles and mining equipment (not currently offered via any RTO for this Diploma level unit).
· AQF level 6: Nothing exists in terms of units at this Advanced Diploma level.
Pathways to achieving competence
Arguably the single-biggest challenge identified has been how to find a balance between compliance and practicality – considering cost, operational interruption, available pathways for delivery of competence and ongoing ease of maintaining compliance.
Most mining operations are looking for cost-effective, sustainably achievable and value-adding training solutions and find it unacceptable to expect every member of their management structure to have to undertake accredited, RTO-delivered units of competency – which under Queensland coal mining regulations require refresher training every five years. At the other end of the spectrum, some operations believe that on-the-job experience is the best source of competence, replacing any need for formal training.
The authors believe the truth lies somewhere in between and have proposed a practicable solution for SSE’s to consider and include in their rationale for application of RS22.
Hierarchy of competency
It is largely accepted that formal qualifications from a recognised authority is best practise to demonstrate competence. In the context of RS22 compliance at mining operations, the authors have identified that this can generally be achieved one of three ways, presented as 1a, 1b and 1c in Table 1, however, achieving this can be difficult, slow and disruptive to operations.
TABLE 1
Hierarchy of competency.
RS22 does not explicitly demand full qualifications or a Statement of Attainment (SoA) for RII units, nor does it specify a time frame to achieve this result, therefore the authors set about defining a pathway through a ‘hierarchy’ of ever-increasing ‘quality’ to demonstrate competency. These lower hierarchies (listed as 2, 3 and 4 in Table 1) provide faster, less disruptive and resource intensive alternatives.
Target pathway
The final step is for the SSE to define the minimum acceptable hierarchies for competence and to do so over a timeline – we call this the ‘pathway to competence’.
A typical pathway from amongst the case studies is shown in Table 2.
TABLE 2
Typical pathway to competence.
Corporate resilience
Overall corporate resilience was found to be poor across all mining operations – which is perhaps not surprising given how new the RS22 framework is and the challenges faced by sites in simply obtaining the necessary competencies in the first place.
The various sources of ‘never-ending change’ are represented in Figure 1 – note that a change in any one or more of these sources should trigger a review of RS22 management structure and likely result in changes and a new notification to the Qld Mining Regulator. Therefore, it is critical to have a system in place to monitor for changes and react appropriately and in a timely manner.
FIG 1 – Sources of ongoing change.
Other findings
· Not everyone on the Management Structure should be there – it is not the same as the ‘organisation structure’, which normally has positions such as human resources manager, finance manager, IT coordinator and others who generally do not directly have an SHMS related role affiliation.
· Each position on the management structure is unique – every role has unique SHMS related responsibilities, which means it’s not appropriate to simply group all the supervisors into a single role and have one list of competencies for them all.
· Most surprising was that no mining operation used as a Case Study was using software to determine MUE’s, maintain their fluid management structure and track the competencies required and provide compliance to RS22. This was witnessed as highly reactive, time-consuming and manual-based solutions, that were error prone and easily outdated.
TRANSFERABILITY TO OTHER LEGISLATIVE FRAMEWORKS
The legislation of each state in Australia prescribes roles with competency requirements. The approach across all states is somewhat inconsistent, that is, some states have applied selected parts of the model WHS Act to mining and repealed their mining specific legislation while other states have either partially or wholly maintained their mining specific legislation or mining specific requirements, for example Queensland and New South Wales have maintained a very specific mining related focus. A cross comparison of different Australian State and Territory Work Health and Safety (WHS) legislative frameworks is provided in Figure 2 – note the overlap and gaps in approach.
FIG 2 – Safe Work Australia Model WHS Act cross comparison table showing variation and inconsistency.
Although RS22 was specifically developed from Resources Safety and Health Queensland, the concept and process are highly transferrable to any location and industry and can be used to ensure that people are competent to perform their roles and activities.
To apply this process to any industry in any location, the same methodology applies as detailed in Section 3 of this paper can be used along with a jurisdiction specific mapping exercise to identify:
· relevant legislation
· legislatively identified roles
· legislatively identified competency and/or licensing requirements
· legislatively identified risk management systems
· organisational risk management documentation.
Statutory roles
A comparison of competency and licensing requirements for a mine in Queensland versus New South Wales found that for the statutory roles identified, where these or similar roles exist in other jurisdictions, the duty holder from the relevant legislation would generally have the requirements under that particular legislation (May, 2024).
General considerations
Irrespective of the statutory/licensing requirements, it should be recognised that the approach put forward by the authors provides a well-considered process to ensure the Management Structure is established with a well thought out rationale to ensure competence to provide a safe place of work – which would likely meet the expectations of all jurisdictions across Australia and overseas.
DISCUSSION AND CONCLUSIONS
Overall, initial compliance with RS22 was found to be limited across the Queensland mining operations, both open cut and underground. Existing training systems worked well at AQF level 3 and below (trades and coalmine workers/equipment operators) but failed to consider all but the most generic competencies required by supervisors and above.
Demanding full qualifications or RTO-delivered RII units is prohibitive and so a ‘pathway to competence’ through a hierarchy and a defined timeline is recommended.
Given the continuous, ongoing changes with the management structure witnessed by the authors across each mine operation because of ‘never-ending’ change in people movements, site risk profiles and the corresponding time-constrained reporting/notification requirements under legislation it is now imperative that software-based solutions are considered to maintain compliance in a timely manner. Software-based solutions are increasingly being relied upon to address the needs of SHMS regulatory requirements and the significant administrative load placed on the SSE as a result, whilst allowing the coordination of efforts across multiple departments and sites for mining operators.
An example the purpose-built Software My Competency ExpertTM, version 1.3 (by Zen Meerkat) is provided in Figure 3 – note the dashboard for operator interface, reference to RS22 with an update metric showing compliance and the exemplar of how to manage change to personnel in the management structure.
FIG 3 – Various tools available via software-solutions. Clockwise, from top: Overall site compliance dashboard (ongoing compliance), recommendations for replacement of employee leaving the company (succession planning) and ongoing change (corporate resilience). (Source: My Competency Expert (My Competency Expert, 2023), 2023).

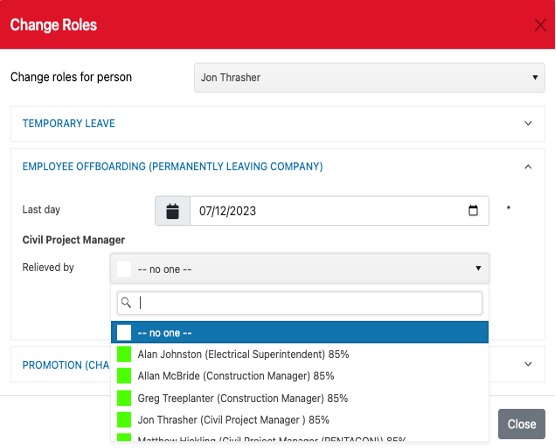

ACKNOWLEDGEMENTS
The authors acknowledge the invaluable support of the individuals within the mining companies who worked with us to develop various solutions to understand, implement RS22 – in particular Tom O’Connor from Pembroke Resources and Graeme Furnell from Bravus Mining and Resources, who provided valuable feedback and helped created a more balanced approach for a sustainable, efficacious and practicable solution.
REFERENCES
Recognised Standard 22 (August 2021) Resources Safety and Health Queensland. Available from: <https://www.rshq.qld.gov.au/resources/documents/mines-resources/safety-and-health/legislation,-standards-and-guidelines/recognised-standards-coal-mines/recognised-standard-22.